Have a Good Day with Finning
Happy is a day when things go right. When the wheels turn, the engines roar and the work gets done.
Built to be rebuilt – the process.
It’s well known across the industry that Cat® machines are ‘built to be rebuilt’ - giving customers the opportunity to save thousands, boost their sustainability credentials, and give their machines a second, third or even fourth lease of life.
We recently caught up with Mark Tudball, Product Manager for rebuilds who gave us an insight into the step-by-step process involved in rebuilding a machine.
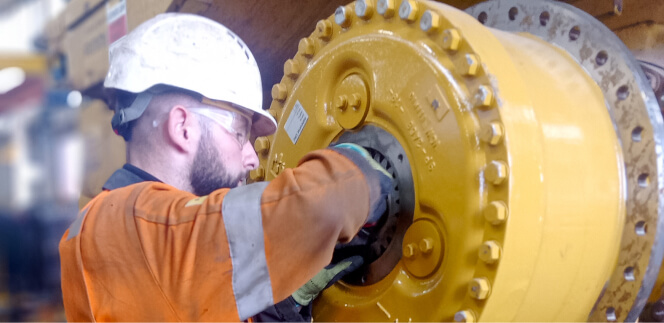
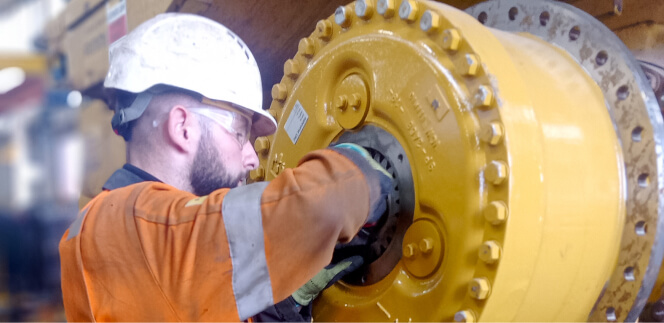
PART 1: MACHINE PRE-REPAIR INSPECTION
Our specialist rebuild engineers begin by carrying out a full machine inspection (called Cat Inspect). This involves bringing the machine into the service workshop for inspection, dropping the belly guards, taking all panels off, washing down to remove any debris that’s on the machine – in line with contamination control guidelines.
PART 2: WORKSHOP STRIP DOWN
The machine is lifted onto stands in the workshop and the engineers disassemble all external and internal components from the machine. This process typically takes around a month with all major components, including the cab, blade assembly, ripper, track frames, and all the power train elements such as the transmission being removed.
PART 3: IN-DEPTH INSPECTION
Now that the main components have been removed the engineers can carry out a more in-depth inspection looking along the chassis, inspecting the state of the hose work and identifying any damage to the mounts or brakes. Once this has been done Finning prepares its recommendation of the full scope of work required – over and above the type of rebuild already agreed – and provides a cost and timeframe for the work.
Once the full scope of work is agreed with the customer, Finning will manage the logistics of the rebuild process. This includes ordering all the major components needed for the rebuild so that the engineers have access to them when they need them.
PART 4: REASSEMBLY STAGE
Once the major powertrain elements are refitted and the cab reinstalled on the machine, everything is connected, oil and coolant topped up ready to start the machine. This ensures there are no leaks, and that all components are fitted and working as they should. It also provides the opportunity for the engineers to identify any glitches or issues – while the machine is still in a part assembled state and some of the more complex parts of the machine accessible.
Depending on the type of machine, the final reassembly will be made. For a Dozer it would now be time to put the track frames back on, using engine drive to reconnect the track link assemblies, and reinstall all the panels and reassemble the blade and ripper. Any additional guards or cameras are also installed at this point.
PART 5: PERFORMANCE INSPECTION
The performance testing is one of the final critical phases of the rebuild. It enables the team to identify any final fine tuning needed to ensure pressures are all within Caterpillar specifications when operated within its normal machine configuration. The testing includes hydraulic system checks incorporating pump pressure checks, and cylinder cycle and drift tests. As well as running the engine up to temperature and putting the engine/transmission into stall conditions to pressure test of major components. Note the exchange units will have already been tested.
PART 6: THE FINISHING TOUCHES
During this final phase, the machine is fully washed, and any belly guards added ready for its paint job. The finished, gleaming machine is then handed back to the customer.
The rebuilt machine is expected to continue to operate for another 15,000 - 20,000 hours – then it can be rebuilt again!
To find out more about the Finning rebuild service, or to register your interest in having a machine rebuilt, visit: https://www.finning.com/en_IE/services/response-repair-rebuild/rebuilds.html
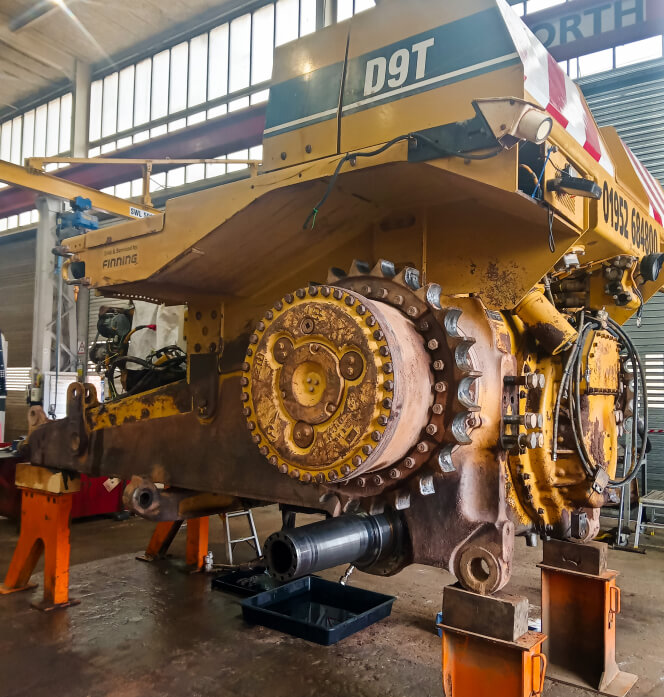
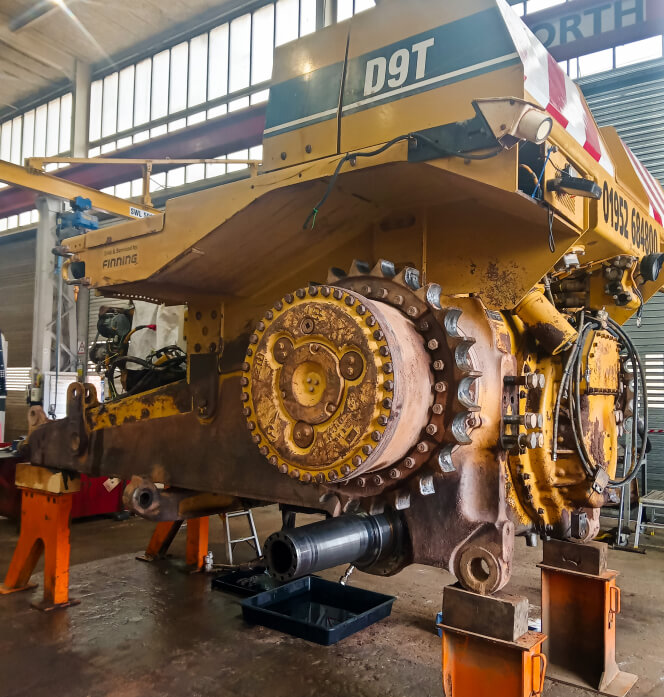

