Have a Good Day with Finning
Happy is a day when things go right. When the wheels turn, the engines roar and the work gets done.
An insiders view of a rebuild of a Cat® D6
With cost and sustainability pressures steadily growing across our industry, choosing a rebuild, rather than replacing, plant machinery not only makes commercial sense but its good for the environment too. Here Paul Reddish, Workshop Customer Service Controller at Finning UK & Ireland, reveals how the company’s team of engineers at its Chesterfield branch breathed new life into a beloved Cat® D6 Dozer owned by Smiths Construction, resulting in significant cost savings and a machine that looks and operates as good as a new one.
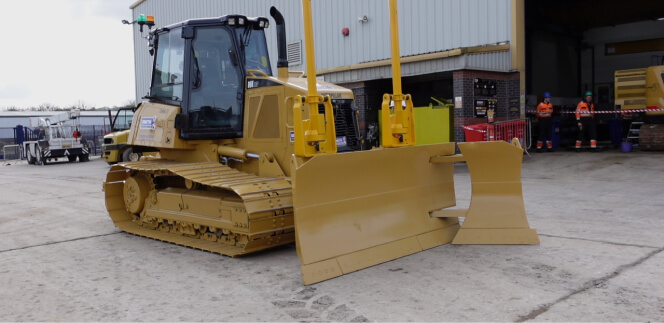
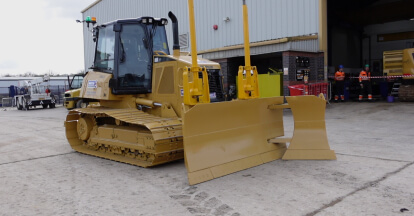
Smiths had been running its trusted Cat D6K dozer for 16 years during which time it clocked up over 8,700 hours carrying out general ground and landscaping works. Despite being regularly serviced and maintained, the time came when the powertrain and hydraulics on the machine were beginning to show signs of wear and tear which was starting to impact on its operational performance and efficiency.
After an initial consultation, we recommended Smiths consider a ‘Cat Certified Rebuild’ instead of buying a new machine and it was booked into the Chesterfield workshop to carry out the work.
We treat every machine rebuild as unique. Which means we put the machine under the microscope and carry out a thorough pre-rebuild inspection. During this we were able to identify wider issues with some of the machine’s systems and components. For example, we spotted excessive play in the pins for the blade lift and twist mechanisms. The inspection we carry out is very thorough and highlighted smaller problems from missing bolts on the under guards to an inoperative back rest adjustment on the operator seat.
A powertrain rebuild involves reconditioning the final drives and brakes, cleaning and testing the existing radiator pack and replacing the drive pump coupling with a new unit.
As part of the certified rebuild specification on this machine, around 3,000 individual parts like hoses, gaskets, belts, seals and wiring were replaced with new ones. The remaining components, forming the main bulk of the engine, were individually inspected to assess their condition which was measured against strict reusability guidelines. Many of the parts needed replacing, in some cases brand new parts were ordered, but most were either reconditioned on site, or sent off to be remanufactured.
Part of the rebuild included addressing the severe wear on the engine's crankshaft after years of operation had resulted in significant scoring and out-of-round conditions on the main and rod journal surfaces. A Cat Reman engine was used to replace the existing engine having already been completely reconditioned. In turn, the existing engine from the D6 was sent to Caterpillar to be remanufactured.
For the hydraulic rebuild, the motors, pumps and oil cooler were treated in the same way as the engine, with part-by-part reconditioning, replacement or remanufacture. Hoses, couplings and cylinder seals were replaced with new components. The main control valve and hydraulic tank were reconditioned.
The control valve required significant attention. Years of exposure to contaminated hydraulic fluid had resulted in erosion of the spool lands and bores. To address this, new valves, seals and solenoids were fitted.
As well as applying their engineering skills to meticulously follow Caterpillar specifications, the Finning rebuild team were mindful of the need to keep the customer updated on the progress of the project throughout. This involved filming walk-around videos with commentary detailing the work completed, which were sent to Smiths on a weekly basis.
This exemplifies how the Caterpillar rebuild philosophy, permeates through the Finning team to the customer. It is important to remember that people really care about their machines, and the decision to rebuild is not just a financial one. The business benefits in this case however, are unequivocal. Rebuilds cost around 50-75% of the price of a new machine and include a 5-year powertrain and hydraulics warranty.
With all the recommended maintenance work carried out, and a visit to the paint shop, this 17-year-old D6 dozer looks and works like new. Giving this machine a second life makes sense, and also feels good, for everyone involved.
To find out more about insiders view of rebuild go to Visit our Digital Toolbox overview for our latest offers and news.

